What is Lean Six Sigma in Hawaii?
Contact Us
Are you interested in Lean Six Sigma?
Six Sigma was established in 1987 when Motorola unveiled its initiative. Over time, the quality control strategy shown has had an interesting growth curve. It began slowly but later gained favor as a result of its impressive potential. Six Sigma was noted to have significant early growth potential during the 1990s when Jack Welch, then the CEO of General Electric, and now the AlliedSignal CEO, adopted the technique. Several companies since then have embraced and reaped the gains from this strategy.
Six Sigma used to be referred to as a “management fad” in the mainstream view, and not a “quality control system”. The effect is six sigma, which has resulted in billions of dollars in return on investment for Fortune 500 companies. Today though, it is known that it is not a fad in management anymore.
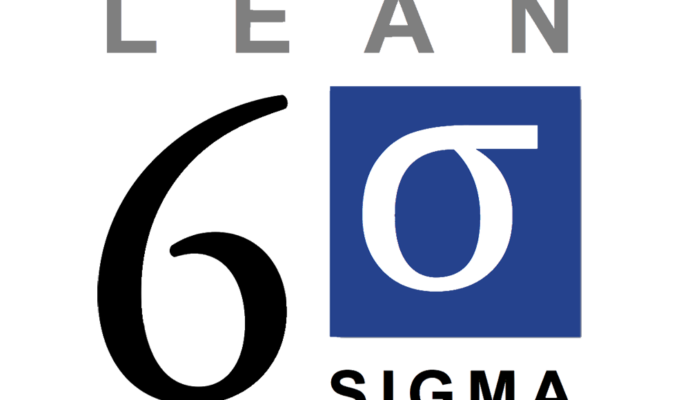
The Benefits of Using Lean Six Sigma
Using Six Sigma results in substantial savings in time, resources, and improved accuracy. The Six Sigma approach is frequently successful when used carefully and conscientiously. Fosters a sense of market well-being and retains customers: Every profitable company aims to preserve its current client base. Clients would choose to stick with your company instead of trying another service or switching to a competitor’s brand. Do you take into consideration the customers who are unhappy with the services you’re offering? Many companies will be unaware of this reality and prepare business growth strategies without realizing that consumer satisfaction should always be considered.
By using the Six Sigma process, risk has been removed. To efficiently engage consumers, conduct a dipstick survey to ascertain the required features of your service or product. When developing your business development strategies, make sure you will not forget something that could entice your customers.
The current market needs an integrated strategy of business intelligence, performance, advanced technology, and robust quality control. Would you like your company to be considered as one of the industry leaders? Will you plan to achieve a major competitive edge in your industry’s marketplace? Using Six Sigma methodologies will maximize the productivity of the available capital assets.
FAQ’s
The future is bright. The rate of change increases with each passing year. The primary function of management in an organization is to design and implement systems. Development and value-making with most systems for customers and businesses. This is a never-ending process. To retain customers, you must innovate to attract them. Delivery innovations change the way products and services are provided to customers. Customer preferences will rapidly evolve. Today's pleasure turns into a need tomorrow. The shift is recognized by all organizations. It is more imperative than ever for organizations to rise to the task of reform because they must either adapt or perish. Lean and Six Sigma welcomes the change. Both accuracy and timeliness are promoted by this principle. Innovation has to be applied to product and service strategies. Operational improvement isn't a procedure, it is a way of life. The paradigm of "Lean Six Sigma" (a list of management tactics and best practices). Managers can use these as guidelines for potential change. Both operators and engineers are Black Belt candidates and all applicants for operator and engineer positions are screened for being Black Belt material. This implies that Six Sigma is on course and on track with company strategies. Given the importance of finding the right Lean Six Sigma partner, it only seems natural to ask more frequently asked questions of all the others. Here are some of the most commonly asked questions, and here are some of the answers you can expect. At the very least, our Lean Sigma partner has an active Six Sigma consultant, who can provide instruction and coaching for your Master Black Belt. A Master Black Belt would need real-world skills and be comfortable with your company's environment and people. in the process of preparing, candidates can develop strategies and apply them to programs in the real world. Sometimes, course assignments demand that the trainees be connected to project results for learners to be able to put their expertise to practical use. It includes dollar realizations and schedule lagging, to ensure that projects remain on budget and on time. Participant and systemic issues should be defined by the Master Black Belt. To make meaningful progress, it is important to recognize the readiness of the company to adopt Lean Six Sigma. Your implementation partner should outline preparatory activities that lay the groundwork for ongoing deployment. This includes analyzing ongoing projects and programs in the pipeline, as well as defining plans for future initiatives. A gap report should provide a review of defined priorities as well as an overview of customer and business knowledge. This aspect helps in identifying potential implementation problems, which can be dealt with. Mathematical approaches are used to certify the six sigma metrics and outcomes Six sigma figures are focused on inferential statistics and probability theories. Six sigma is about more than mere numbers. It is a plan that consists of many methods for defining the customer requirements and measuring services. One thing that can be said in favor of Six Sigma is that it eliminates the number of surprises, which helps managers to have a better picture of what “good” looks like and lets them measure performance in the eyes of consumers with more objectivity. To be a Six Sigma practitioner, you must have a strong desire to have excellent customer service, the ability to conduct a baseline analysis regularly and be able to demonstrate statistics. Why Six Sigma?
How Does Lean Six Sigma Operate?
How do you manage project-oriented classes?
How can you incorporate your program with the work that our company is already doing?
Six Sigma is about statistics, do I need to learn statistics?

What is the difference between Six Sigma and Lean?
A cost-effective way of accomplishing mission goals is referred to as the Lean approach (called Muda in Japanese). Taiichi Ohno lists seven stages of waste in operations (TPS fame). Upgrading the service and identifying and eliminating waste is imperative to serving customers.
The Lean and Six Sigma methodologies are used to improve operations and the company. The Lean philosophy emphasizes improving flow, balancing systems, and increasing efficiency. Six Sigma is about development, improvement, and efficiency, and effectiveness.
There are so many areas or regions where we offer these services with most of them being cities.
However, if you need any of these services, you need to contact us. The list below comprises the areas where we offer these services.